Utilizing Life Cycle Assessment to implement Circular Economy strategies in the Steelmaking Industry
A key aspect of the ALCHIMIA project is the quantification of the environmental sustainability of solutions within the steel sector. Life Cycle Assessment (LCA) stands out as a prominent method for evaluating the environmental impact of steelmaking. LCA analyses often intersect with investigations into circular economy (CE) practices in steel production and recycling. Various CE strategies can be implemented in the steel sector [1]. A critical review of the scientific literature has been conducted within the ALCHIMIA project to define the state-of-the-art of the application of LCA to the implementation of CE strategies in steelmaking [2]; from this study, it is possible to retrieve possible recommendations for the researchers involved in ALCHIMIA consortium and other research projects focused on steelmaking.
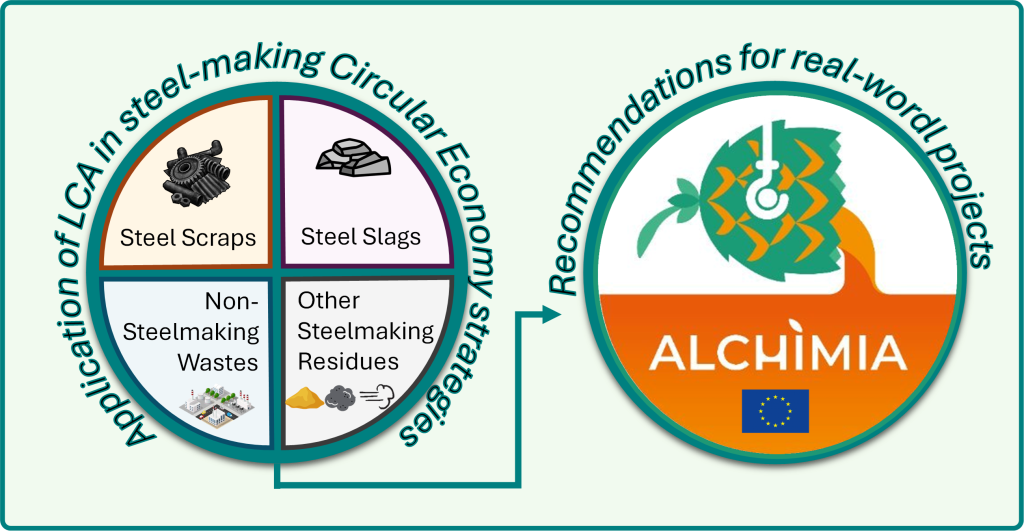
ALCHIMIA focuses on producing secondary steel from scraps. Research papers in the literature underline the importance of addressing scrap quality issues, noting that cleaning scraps during pre-treatments can enhance quality and reduce energy consumption in steel foundries by up to 45% [3]. Additionally, the recovery of valuable materials from steel slags and dust is highlighted as an effective circular practice in steelmaking projects, offering relevant environmental benefits from the recycling of chromium [4] and zinc [5], as well as the production of high-quality direct reduction iron from steel slags [6]. Alternatively, recycling foundry sands and steel slags in the construction sector can reduce the environmental impacts of cement production by more than 40% [7]. Also, the literature analysis suggests exploring energy recovery and secondary carbon sources and reducing agents in industrial symbiosis schemes, which could lead to significant reductions in greenhouse gas emissions within industrial districts, estimated at around 20% [8].
[1] Rieger, J., Colla, V., Matino, I., Branca, T.A., Stubbe, G., Panizza, A., Brondi, C., Falsafi, M., Hage, J., Wang, X., Voraberger, B., Fenzl, T., Masaguer, V., Faraci, E.L., Di Sante, L., Cirilli, F., Loose, F., Thaler, C., Soto, A., Frittella, P., Foglio, G., Di Cecca, C., Tellaroli, M., Corbella, M., Guzzon, M., Malfa, E., Morillon, A., Algermissen, D., Peters, K., Snaet, D., 2021. Residue valorization in the iron and steel industries: Sustainable solutions for a cleaner and more competitive future Europe. Metals (Basel), 11, 1202.
[2] Rossi, F., Niero, M., Frey, M., 2024. Application of LCA to circular economy strategies in steelmaking industry: state-of-the-art and recommendations. Submitted to the XVIII Conference of the Italian LCA Network (Associazione Rete Italiana LCA).
[3] Haupt, M., Vadenbo, C., Zeltner, C., Hellweg, S., 2017. Influence of Input-Scrap Quality on the Environmental Impact of Secondary Steel Production. J Ind Ecol 21, 391–401.
[4] Buyle, M., Maes, B., Van Passel, S., Boonen, K., Vercalsteren, A., Audenaert, A., 2021. Ex-ante LCA of emerging carbon steel slag treatment technologies: Fast forwarding lab observations to industrial-scale production. J Clean Prod 313, 127921.
[5] Ng, K.S., Head, I., Premier, G.C., Scott, K., Yu, E., Lloyd, J., Sadhukhan, J., 2016. A multilevel sustainability analysis of zinc recovery from wastes. Resour Conserv Recycl 113, 88–105.
[6] Nurdiawati, A., Zaini, I.N., Wei, W., Gyllenram, R., Yang, W., Samuelsson, P., 2023. Towards fossil-free steel: Life cycle assessment of biosyngas-based direct reduced iron (DRI) production process. J Clean Prod 393, e02049.
[7] Gauffin, A., Andersson, N.Å.I., Storm, P., Tilliander, A., Jönsson, P.G., 2017. Time-varying losses in material flows of steel using dynamic material flow models. Resour Conserv Recycl 116, 70–83.
[8] Dong, H., Ohnishi, S., Fujita, T., Geng, Y., Fujii, M., Dong, L., 2014. Achieving carbon emission reduction through industrial & urban symbiosis: A case of Kawasaki. Energy 64, 277–286.