Transforming Metal Production with the ALCHIMIA Project: Innovations in Scrap Characterisation and Process Optimisation
The European project ALCHIMIA is setting a new benchmark in metal production by focusing on 3 Celsa steel plants located in France, Spain, and Poland. This initiative aims to develop advanced tools for scrap characterisation, process monitoring, optimisation, and decision support. These tools will be integrated into a comprehensive AI framework, designed to enhance the economic impact and environmental sustainability of metal-making processes.
Enhancing Scrap Characterisation and Charge Mix Optimisation
One of the core innovations of the ALCHIMIA project is the charge mix optimisation tool. This tool is engineered to select the most eco-friendly and cost-effective mix of scrap types and alternative charge materials necessary for producing various product qualities, such as liquid steel ingots. The optimisation process considers several factors:
- Purchase Costs and Energy Supply: The tool evaluates the purchase costs of different scrap types along with the energy required to melt them down. This dual consideration ensures that the selected mix is both economically viable and energy efficient.
- Environmental Impact: The environmental footprint of each scrap type is a critical factor in the optimisation process. By considering the environmental impact, the tool ensures that the chosen mix aligns with sustainability goals.
- Operational Restrictions: Practical constraints such as the volume of the charging vessel and the maximum allowable amounts of certain scrap types are factored into the optimisation process.
- Real-Time Availability: The tool connects to an online inventory control system to access real-time data on the availability of different charge materials. This dynamic approach ensures that the optimisation process is grounded in current supply conditions.
Advanced Monitoring and Predictive Modelling
The ALCHIMIA project leverages advanced mathematical models and AI-assisted optimisers to monitor and predict the behaviour of the steel melting process. These hybrid dynamic models combine energy and mass balance calculations, enabling several key capabilities:
- Continuous Temperature Calculation: By considering the specific meltdown energy demand of the charged materials along with electrical and chemical energy inputs, the models provide continuous calculations of the melt temperature.
- Metallurgical Reaction Modelling: The models simulate the metallurgical reactions occurring during the melting and refining processes. This allows for the continuous calculation of the metal melt’s chemical composition, ensuring precise control over the quality of the produced steel.
Conclusion
The ALCHIMIA project is at the forefront of revolutionising metal production through its innovative approach to scrap characterisation and process optimisation. By integrating these advanced tools into an AI framework, ALCHIMIA not only improves economic outcomes but also champions environmental sustainability. As the project progresses, it promises to set new standards in the metal-making industry, paving the way for a more sustainable and economically viable future.
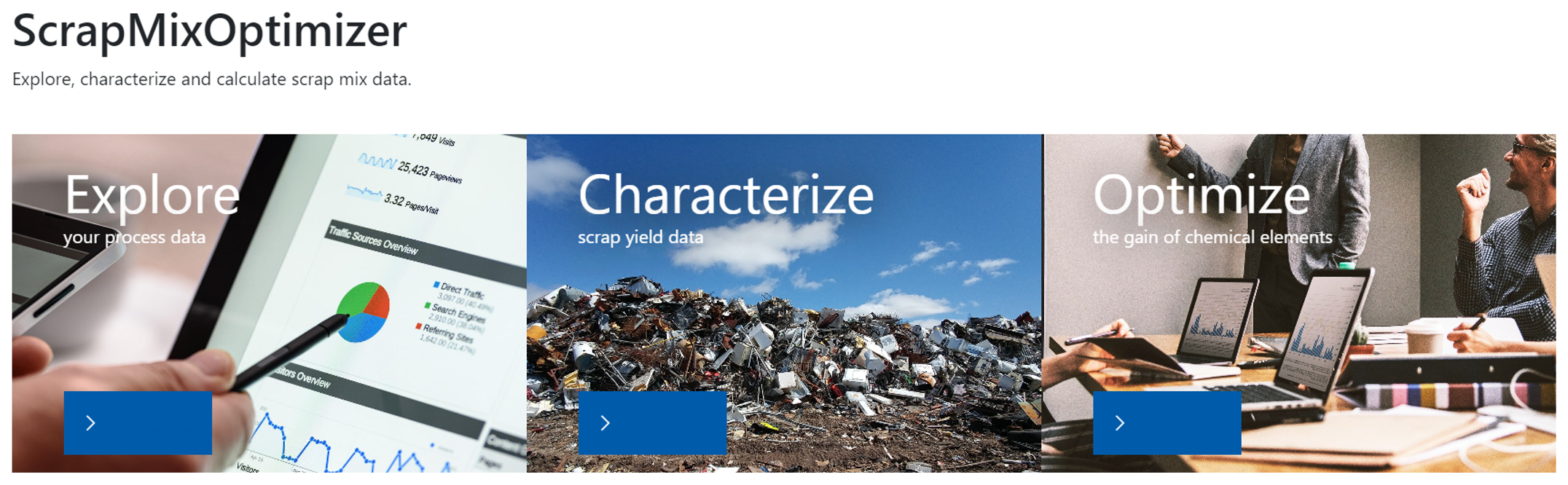