Pilenga Baldassarre Foundry Joins the ALCHIMIA Project for a Greener Future
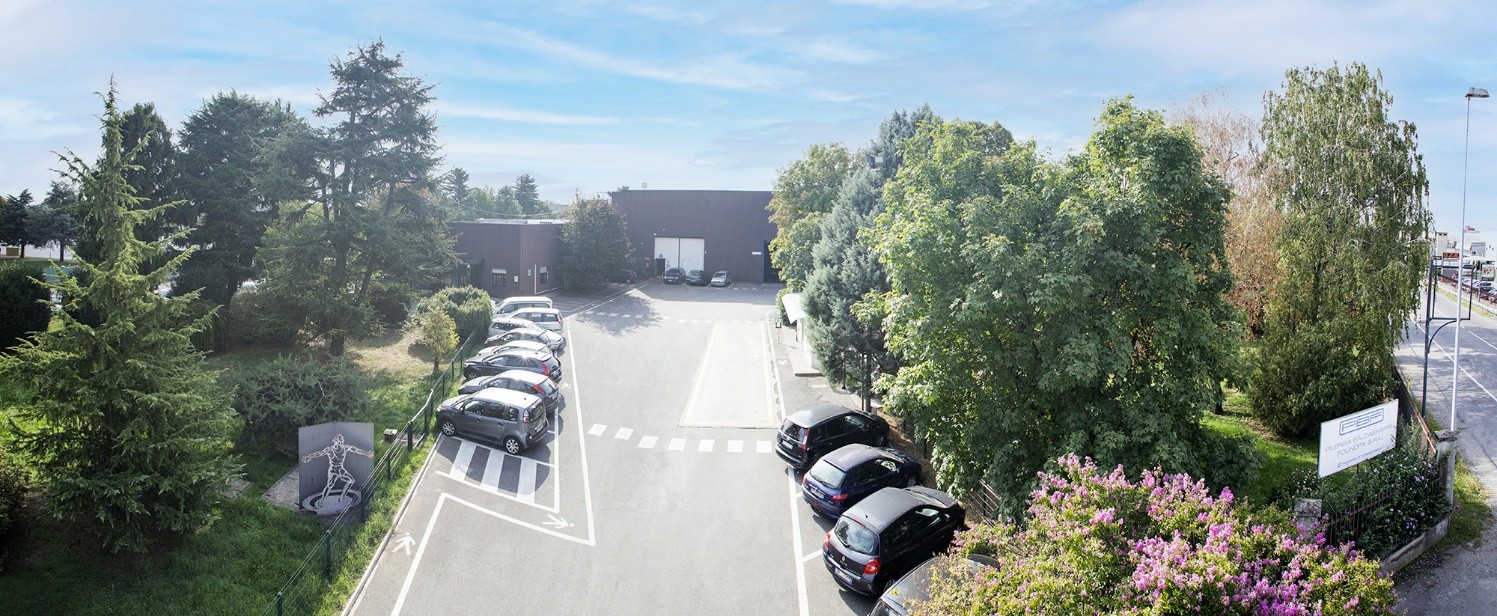
Technological innovation and industrial sustainability take another step forward with Pilenga Baldassarre Foundry joining the European ALCHIMIA project. Following the lead of Fonderia di Torbole, actively involved from the start, the affiliated foundry is now adopting the ALCHIMIA method, demonstrating that the scalability and replicability of the implemented solutions are both real and achievable in different production contexts.
Production Flexibility and a Green Approach
Pilenga Baldassarre Foundry is a cross-market foundry, distinguished by its high production flexibility: the company can manufacture castings ranging from 0.05 kg to 350 kg, serving a wide array of application sectors. This flexibility makes a structured and intelligent data management system strategically crucial.
Environmental sustainability is a cornerstone of the company’s philosophy: optimizing the use of natural and energy resources, responsible raw material management, and the use of recycled materials in the melting process are central to the foundry’s daily operations.
Advanced Quality Control: From Input to Output
The foundry performs thorough monitoring of process parameters from the very first stages, analyzing input data (such as chemical composition and operating conditions) and comparing them with output data, namely the physical characteristics of the final product. This method enables rigorous quality control, based on objective and measurable evidence.
The ALCHIMIA Method: Artificial Intelligence Serving Production
The integration of the ALCHIMIA method adds a new level of innovation, thanks to the use of artificial intelligence technologies that allow for:
- Predicting the quality of the raw casting, identifying potential defects such as porosity, cementite, or the degree of graphite spheroidization in advance;
- Real-time analysis of chemical and thermal data from in-line furnaces;
- More accurate correlation between input and output data, enabling continuous product quality improvement.
One key competitive advantage? The ability to anticipate production outcomes, eliminating the wait for post-process analysis and enabling immediate corrective actions in case of deviations from the optimal process.
Goals and Impacts
The adoption of the ALCHIMIA method is an ambitious challenge, geared toward a low-carbon economy. Expected impacts include:
- Improved energy efficiency;
- Reduced CO₂ emissions;
- Lower quantities of scrap or non-conforming materials;
- Optimization of raw materials and ferroalloys usage;
- Strengthening the circularity of production processes.
Moreover, the use of AI in industrial settings must comply with essential criteria such as safety, data protection, reliability, and real-time performance, ensuring robustness and fault tolerance.
A Shared Path Toward the Future
Pilenga Baldassarre Foundry’s entry into the ALCHIMIA project is not only a technological milestone, but also a statement of values: the company fully embraces the project’s principles, which aim to harmonize performance with sustainability, quality with environmental responsibility.
The synergy between digital innovation and industrial expertise lies at the heart of this journey—one that seeks to redefine industry standards with a green, data-driven vision.