Dynamic process model for Electric Arc Furnace (EAF): A path to smarter, more efficient Steel production
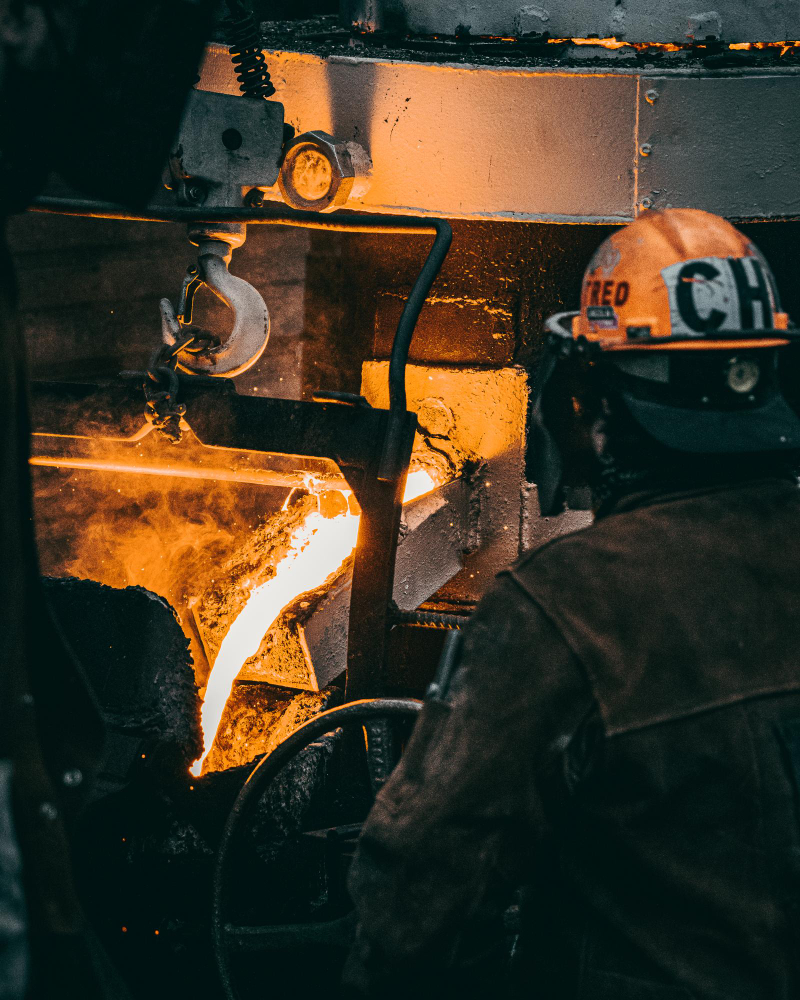
The dynamic process model for Electric Arc Furnaces (EAF) in the Alchimia project is at the forefront of improving steelmaking operations. This physics-based model employs a continuous balance of energy and mass to track and optimize the EAF’s energetic behavior in real-time. Below are key functionalities that help to improve EAF’s performance and drive operational efficiency.
Real-time calculation of melt temperature
By providing the process input parameters, the model enables continuous online calculation of the melt temperature, providing operators with real-time insights into the process. Maintaining the right temperature is crucial for ensuring the quality of the final steel product, and this close monitoring of the temperature conditions help in achieving that. A major advantage of this dynamic process model is also its ability to calculate the meltdown degree of the melt in the furnace.
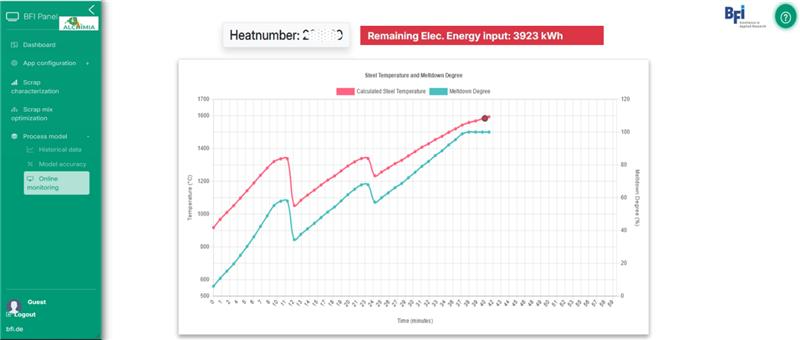
Real-time calculation of chemical composition
The dynamic process model is also crucial in determining the chemical composition of molten steel. By monitoring mass flow and chemical reactions within the furnace, it continuously calculates the melt’s composition. Among these elements, the carbon and oxygen content are particularly important for operators, as their precise control is essential for achieving the desired mechanical properties and minimizing impurities. This level of accuracy is vital for optimizing product quality, ensuring the steel meets stringent standards for strength, durability, and performance.
Model-based process control
At the heart of the dynamic process model is its ability to continuously monitor the state of the melt. By integrating various process inputs—such as electrical energy, oxygen, carbon, and natural gas—the model calculates material composition and temperature, providing operators with real-time insights into the furnace’s energetic behaviour.
A key feature of this model is its model-based control, enabling more efficient resource utilization during the EAF process. For example, by analysing the meltdown degree (as shown in the first image), operators can determine the optimal timing for charging the scrap basket into the furnace. Furthermore, to precisely achieve the target temperature and carbon content in the steel by the end of the process, the model utilizes initial process measurements to dynamically determine the necessary additional electrical energy and oxygen input. Accurately determining these process parameters is essential for maximizing efficiency and avoiding resource overuse. This not only reduces energy costs but also minimizes emissions both critical factors in driving the steel industry toward greater sustainability.
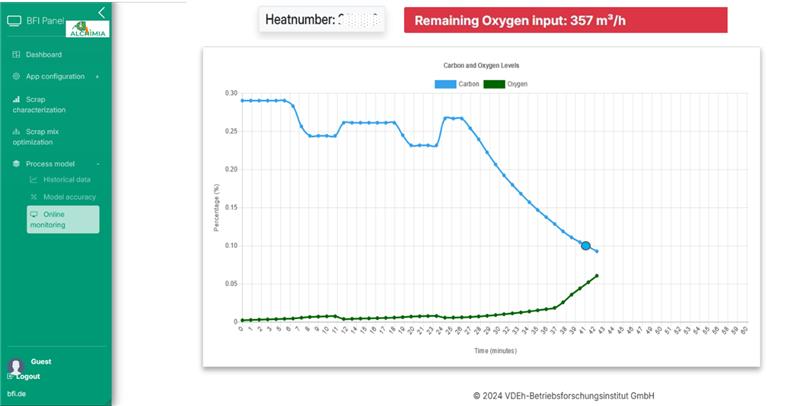
Conclusion: Paving the way for sustainable steelmaking
The dynamic process model for Electric Arc Furnaces offers a robust, physics-based approach to optimizing steel production. By leveraging continuous energy and mass balance calculations, real-time monitoring of the melt temperature, and precise control over the chemical composition of the melt, this model enables smarter, more efficient, and more sustainable EAF operations. As the industry moves towards greener and more energy-efficient processes, innovations like this are crucial in paving the way for a low-carbon future in steel manufacturing.